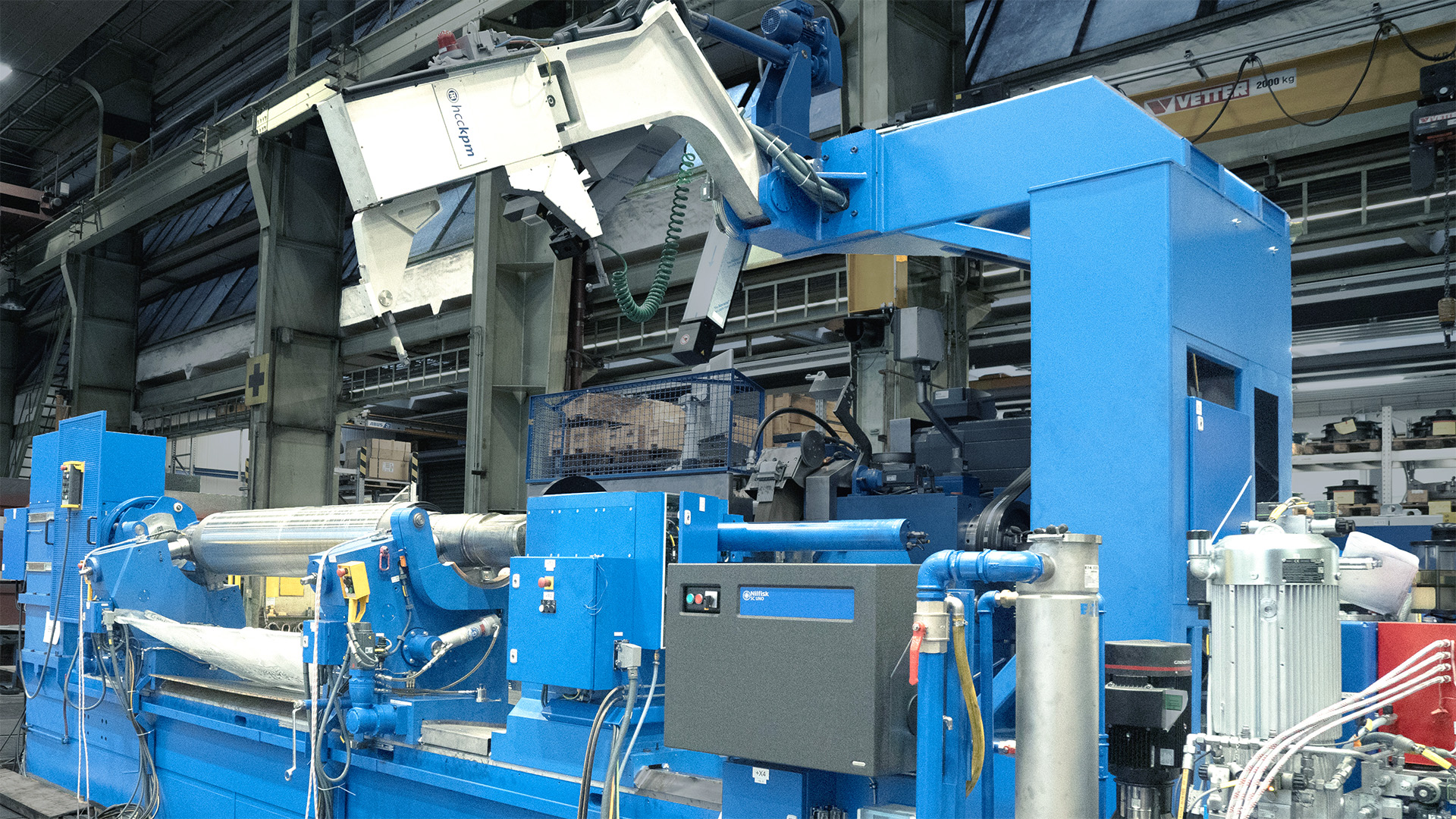
Outstanding Performance and Extraordinary Design Convince Voestalpine
Voestalpine Stahl GmbH is one of the world‘s leading steel producers. With its high-quality products, the company supplies a wide range of industries, such as the automotive and household appliance industries as well as the aviation, oil, and gas industries. In order to reliably and precisely achieve the required quality of the end products, our customer has purchased another machine from the HerkulesGroup for the plant in Linz: A WS 450 × 4500 CNC Monolith™ roll grinder.
Equipped with high-precision HerkulesGroup measuring and control technology, the required roll surface accuracies are achieved with pinpoint precision. Thanks to the intuitive machine control with multi-touch panel in combination with the high-precision C-frame Caliper for roll measuring, corrections are made “on the fly“ during the grinding process.
The design of the grinder impresses with its high mechanical rigidity and damping properties. The heavily ribbed design guarantees the rigidity of the machines. The combination of hydrodynamically and hydrostatically guided ways ensures maximum precision and a long service life. The symmetrical load distribution makes the machines absolutely thermostable. The Monolith™ design also guarantees absolute homogeneity of the roll surface thanks to excellent damping properties for virtually vibration-free operation.
Grinding Carriage with Swiveling Grinding Axis − The Patented B-Axis
The machine is also equipped with a movable B-Axis for complex curve grinding. “The B-Axis of the grinding machine adjusts the position of the grinding wheel to the curve of the roll barrel at a swivel angle of 0.5 degrees,“ explains the responsible sales manager, Tobias Wurm. “This means that in the roll barrel area, the grinding wheel is always guided exactly perpendicular to the roll surface, which ensures continuous full-surface contact between the roll surface and the grinding wheel. Grinding with the edge and therefore undesirable feed marks are eliminated. In addition, the increased stock removal resulting from the full-surface contact between the wheel and roll significantly reduces the grinding time.“
But it was not just the performance and special design of the machine that set Herkules apart from its market competitors: “The smooth implementation and good cooperation throughout the entire project phase, as well as the historically good relationships that we have built up with the customer here on site, were key factors in the decision,“ explains Tobias Wurm.
The assembly and initial start-up of the machine is already complete. The Monolith™ machine is grinding to the customer‘s utmost satisfaction and has been accepted for performance testing, so that final machine acceptance can be expected shortly.