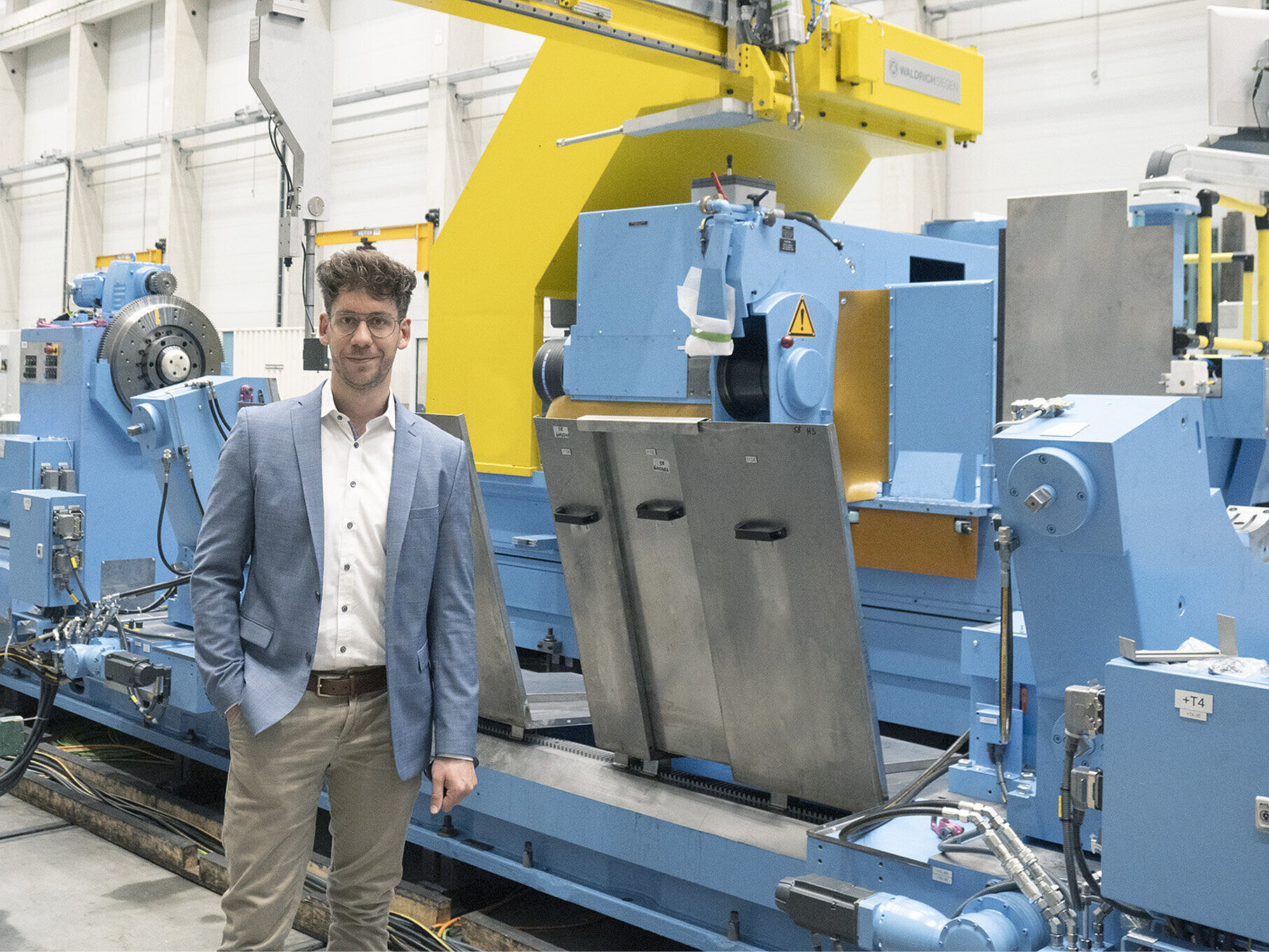
Enormous Increase in Efficiency and High Quality Level for the Best End Product Quality
ProfiGrind Roll Grinders for JSW Steel Vijayanagar and Jindal Steel Odisha Limited
"Our customer JSW Steel Vijayanagar has placed an order with WaldrichSiegen for the fully automated roll shop for the new hot rolling mill including three ProfiGrind 2000 and two ProfiGrind 7500," explains Jannik Schneider, sales representative at WaldrichSiegen. When it comes to grinding work and back-up rolls in the fully automated roll shop, the ProfiGrind series of machines is a particularly good choice: It boasts a high level of quality with regard to the extremely precise grinding results in the μm range and an exceptionally robust design, rigidity and excellent damping thanks to the use of cast components.
"A special feature of the machines is the B-axis integrated in the grinding saddle, which is used for grinding the various curve shapes on the roll barrel and which achieves infeed increments of up to 0.0001 mm by means of eccentric grinding axis bearings," Jannik Schneider explains further. " It guarantees the utmost precision at the highest cutting forces and stock removal rates.“
"To prevent downtimes due to roll defects, the ProfiGrind grinders at JSW Steel Vijayanagar are equipped with a CP measuring device for fully automatic measurement of the roll geometry. The CP measuring arm enables the horizontal alignment of the roll to be precisely determined.
Another large steel manufacturer that has also chosen WaldrichSiegen's roll grinding technology is Jindal Steel Odisha Limited in Odisha, India.
The customer has purchased three ProfiGrind 2000 work roll grinders with distance between centers of up to 6,500 mm, roll diameters up to 900 mm and a roll weight of 20 t, as well as two ProfiGrind 7500 back-up roll grinders with widths between centers of up to 7,500 mm, roll diameters up to 1,600 mm and a roll weight of 75 t for its new steel rolling mill. "All these machines will be installed as a roll shop in the new mill," explains Jannik Schneider. "The fully automated equipment also includes our Modular Roll Shop Management System (MRS) for controlling the roll shop, as well as a loader for handling the rolls and an extensive roll shop equipment package consisting of a washing unit for the bearings, a cooling station for the rolls, a de-chocker and a chock tilter for tilting the chocks to guarantee proper machining of the rolls."
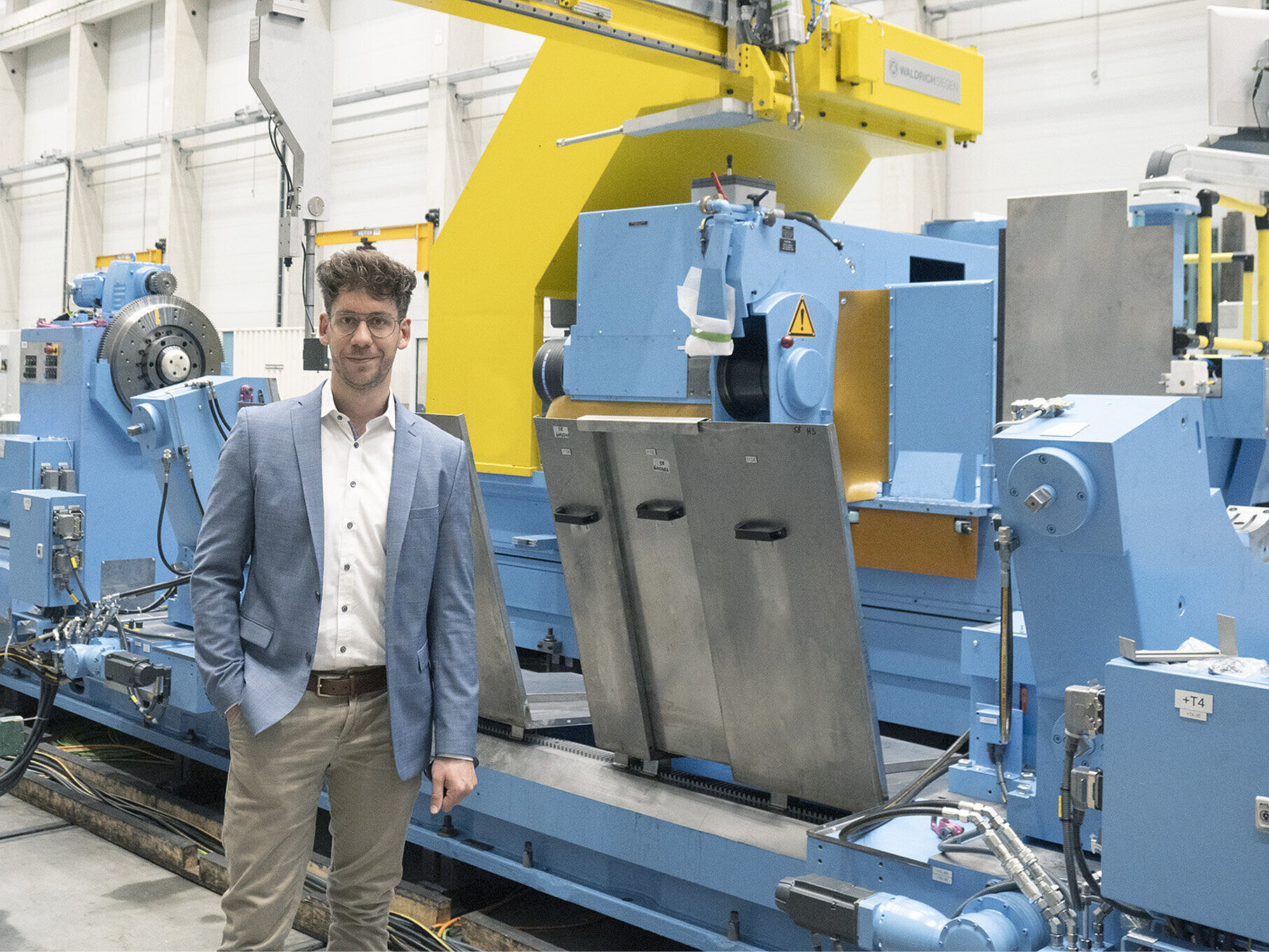
Enormous Increase in Efficiency and High Quality Level for the Best End Product Quality
ProfiGrind Roll Grinders for JSW Steel Vijayanagar and Jindal Steel Odisha Limited
"Our customer JSW Steel Vijayanagar has placed an order with WaldrichSiegen for the fully automated roll shop for the new hot rolling mill including three ProfiGrind 2000 and two ProfiGrind 7500," explains Jannik Schneider, sales representative at WaldrichSiegen. When it comes to grinding work and back-up rolls in the fully automated roll shop, the ProfiGrind series of machines is a particularly good choice: It boasts a high level of quality with regard to the extremely precise grinding results in the μm range and an exceptionally robust design, rigidity and excellent damping thanks to the use of cast components.
"A special feature of the machines is the B-axis integrated in the grinding saddle, which is used for grinding the various curve shapes on the roll barrel and which achieves infeed increments of up to 0.0001 mm by means of eccentric grinding axis bearings," Jannik Schneider explains further. " It guarantees the utmost precision at the highest cutting forces and stock removal rates.“
"To prevent downtimes due to roll defects, the ProfiGrind grinders at JSW Steel Vijayanagar are equipped with a CP measuring device for fully automatic measurement of the roll geometry. The CP measuring arm enables the horizontal alignment of the roll to be precisely determined.
Another large steel manufacturer that has also chosen WaldrichSiegen's roll grinding technology is Jindal Steel Odisha Limited in Odisha, India.
The customer has purchased three ProfiGrind 2000 work roll grinders with distance between centers of up to 6,500 mm, roll diameters up to 900 mm and a roll weight of 20 t, as well as two ProfiGrind 7500 back-up roll grinders with widths between centers of up to 7,500 mm, roll diameters up to 1,600 mm and a roll weight of 75 t for its new steel rolling mill. "All these machines will be installed as a roll shop in the new mill," explains Jannik Schneider. "The fully automated equipment also includes our Modular Roll Shop Management System (MRS) for controlling the roll shop, as well as a loader for handling the rolls and an extensive roll shop equipment package consisting of a washing unit for the bearings, a cooling station for the rolls, a de-chocker and a chock tilter for tilting the chocks to guarantee proper machining of the rolls."
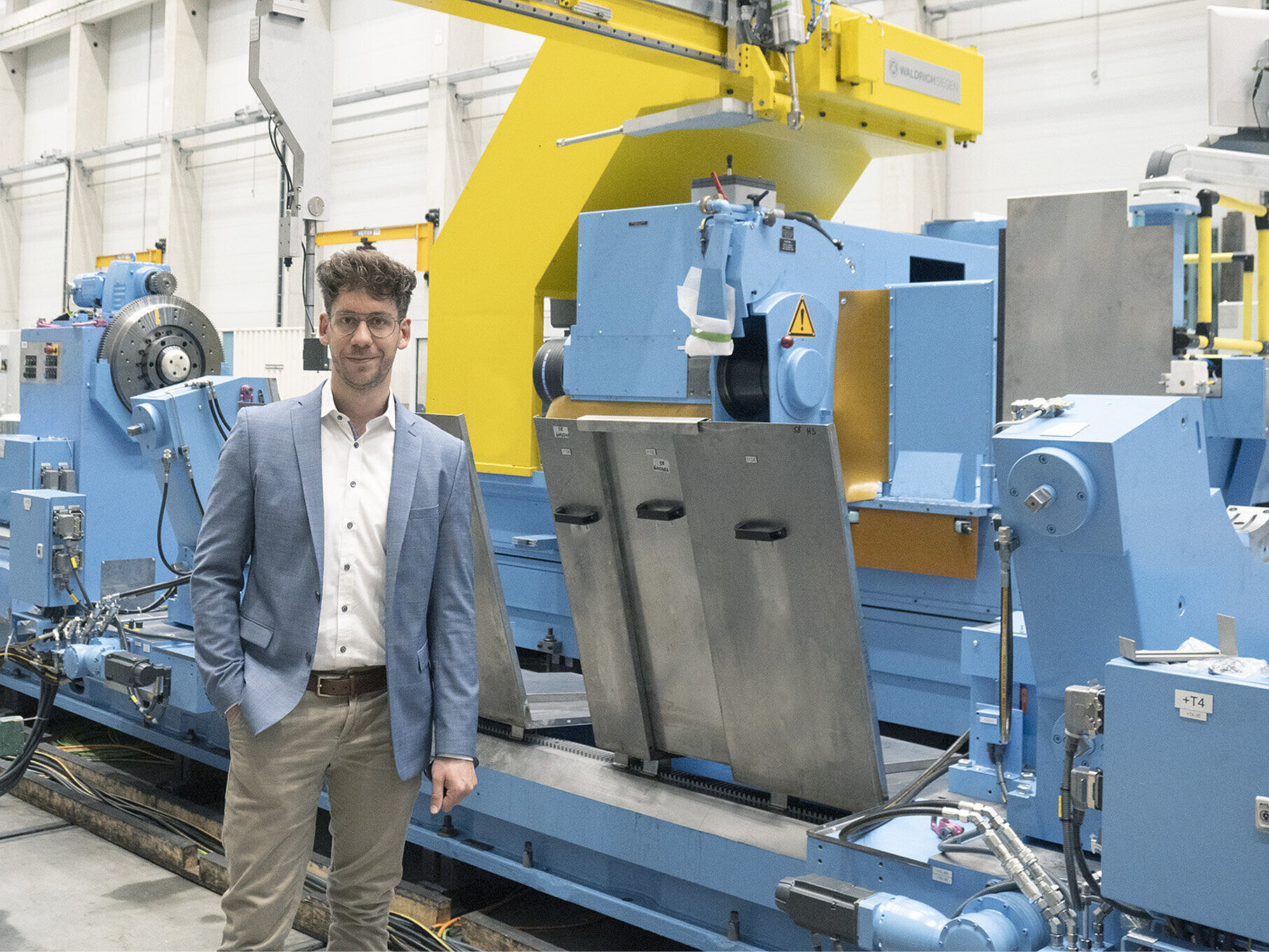
Enormous Increase in Efficiency and High Quality Level for the Best End Product Quality
ProfiGrind Roll Grinders for JSW Steel Vijayanagar and Jindal Steel Odisha Limited
"Our customer JSW Steel Vijayanagar has placed an order with WaldrichSiegen for the fully automated roll shop for the new hot rolling mill including three ProfiGrind 2000 and two ProfiGrind 7500," explains Jannik Schneider, sales representative at WaldrichSiegen. When it comes to grinding work and back-up rolls in the fully automated roll shop, the ProfiGrind series of machines is a particularly good choice: It boasts a high level of quality with regard to the extremely precise grinding results in the μm range and an exceptionally robust design, rigidity and excellent damping thanks to the use of cast components.
"A special feature of the machines is the B-axis integrated in the grinding saddle, which is used for grinding the various curve shapes on the roll barrel and which achieves infeed increments of up to 0.0001 mm by means of eccentric grinding axis bearings," Jannik Schneider explains further. " It guarantees the utmost precision at the highest cutting forces and stock removal rates.“
"To prevent downtimes due to roll defects, the ProfiGrind grinders at JSW Steel Vijayanagar are equipped with a CP measuring device for fully automatic measurement of the roll geometry. The CP measuring arm enables the horizontal alignment of the roll to be precisely determined.
Another large steel manufacturer that has also chosen WaldrichSiegen's roll grinding technology is Jindal Steel Odisha Limited in Odisha, India.
The customer has purchased three ProfiGrind 2000 work roll grinders with distance between centers of up to 6,500 mm, roll diameters up to 900 mm and a roll weight of 20 t, as well as two ProfiGrind 7500 back-up roll grinders with widths between centers of up to 7,500 mm, roll diameters up to 1,600 mm and a roll weight of 75 t for its new steel rolling mill. "All these machines will be installed as a roll shop in the new mill," explains Jannik Schneider. "The fully automated equipment also includes our Modular Roll Shop Management System (MRS) for controlling the roll shop, as well as a loader for handling the rolls and an extensive roll shop equipment package consisting of a washing unit for the bearings, a cooling station for the rolls, a de-chocker and a chock tilter for tilting the chocks to guarantee proper machining of the rolls."
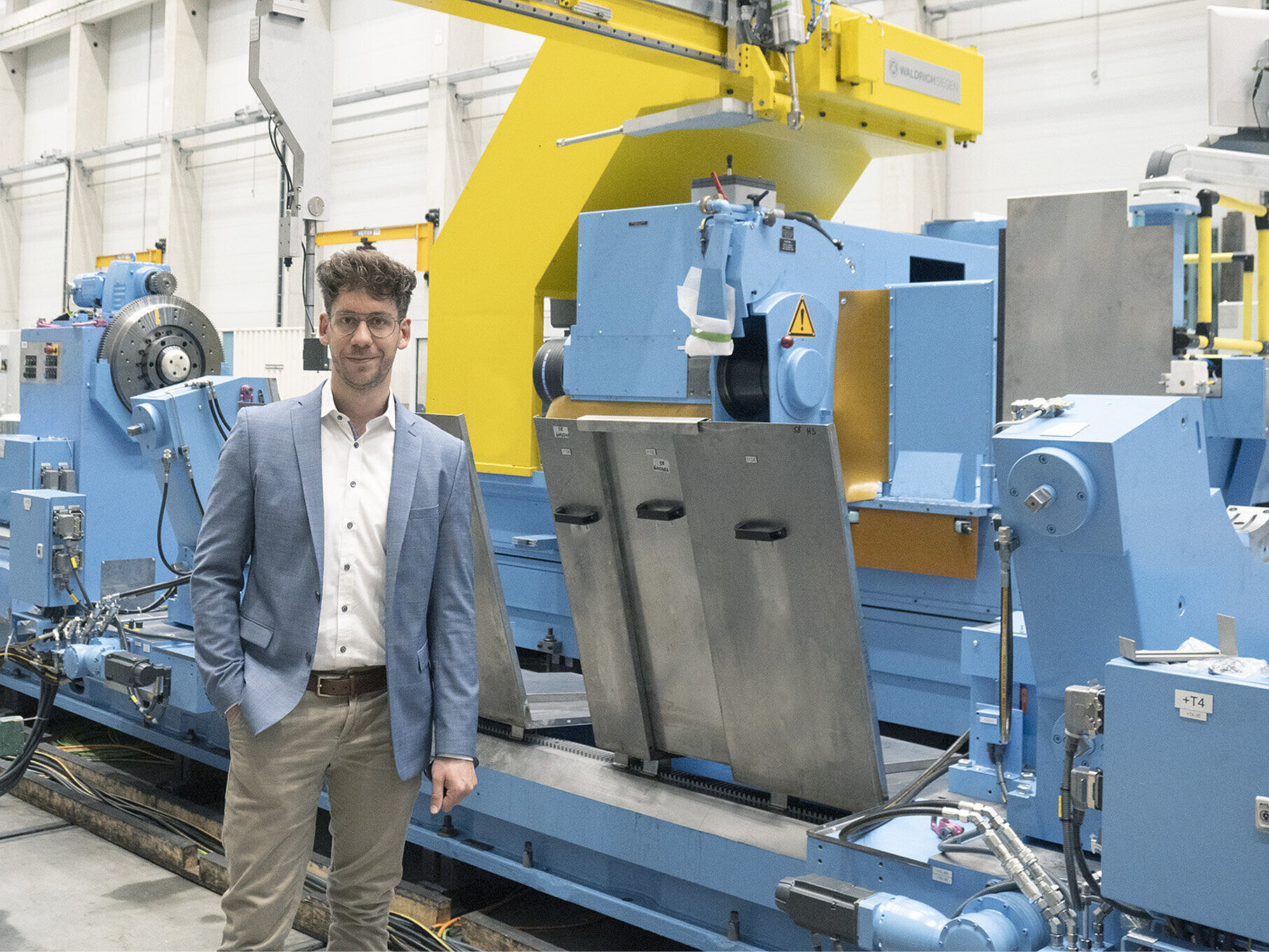
Enormous Increase in Efficiency and High Quality Level for the Best End Product Quality
ProfiGrind Roll Grinders for JSW Steel Vijayanagar and Jindal Steel Odisha Limited
"Our customer JSW Steel Vijayanagar has placed an order with WaldrichSiegen for the fully automated roll shop for the new hot rolling mill including three ProfiGrind 2000 and two ProfiGrind 7500," explains Jannik Schneider, sales representative at WaldrichSiegen. When it comes to grinding work and back-up rolls in the fully automated roll shop, the ProfiGrind series of machines is a particularly good choice: It boasts a high level of quality with regard to the extremely precise grinding results in the μm range and an exceptionally robust design, rigidity and excellent damping thanks to the use of cast components.
"A special feature of the machines is the B-axis integrated in the grinding saddle, which is used for grinding the various curve shapes on the roll barrel and which achieves infeed increments of up to 0.0001 mm by means of eccentric grinding axis bearings," Jannik Schneider explains further. " It guarantees the utmost precision at the highest cutting forces and stock removal rates.“
"To prevent downtimes due to roll defects, the ProfiGrind grinders at JSW Steel Vijayanagar are equipped with a CP measuring device for fully automatic measurement of the roll geometry. The CP measuring arm enables the horizontal alignment of the roll to be precisely determined.
Another large steel manufacturer that has also chosen WaldrichSiegen's roll grinding technology is Jindal Steel Odisha Limited in Odisha, India.
The customer has purchased three ProfiGrind 2000 work roll grinders with distance between centers of up to 6,500 mm, roll diameters up to 900 mm and a roll weight of 20 t, as well as two ProfiGrind 7500 back-up roll grinders with widths between centers of up to 7,500 mm, roll diameters up to 1,600 mm and a roll weight of 75 t for its new steel rolling mill. "All these machines will be installed as a roll shop in the new mill," explains Jannik Schneider. "The fully automated equipment also includes our Modular Roll Shop Management System (MRS) for controlling the roll shop, as well as a loader for handling the rolls and an extensive roll shop equipment package consisting of a washing unit for the bearings, a cooling station for the rolls, a de-chocker and a chock tilter for tilting the chocks to guarantee proper machining of the rolls."